- Home
- Drive Technologies
- Overview Drive Technologies
Tailor-made drive solutions for every application: Efficient electric motors for modern drive technology
Which electric motor is the right one for your application and what makes a good electric motor? Choosing the right electric motor depends on several factors, such as performance, efficiency and, above all, the area of application. This section gives you a clear overview of the different types and technologies of electric motors, how they work and how to choose the right motor for your specific requirements. It also highlights technical advances and efficiency aspects that play a role in deciding on the right drive components.
The most important facts
● Antrimon supports customers in every phase of a project and offers technology-independent, customized drive solutions for various industries and applications.
● Through constant technological progress and innovation, Antrimon develops more efficient drive solutions and helps to reduce operating costs and increase environmental compatibility.
● Careful selection of low-maintenance electric motors is crucial for their longevity and efficiency, and preventive measures and condition monitoring can reduce downtime.
● With state-of-the-art control electronics from the standard portfolio through to customer-specific developments, Antrimon is able to adapt the drive technology precisely to the desired requirements.
We accompany your project from conception and design to series production. Thanks to many years of experience in the drive market as well as specifically trained experts, you can access our comprehensive expertise in every phase of your project. When developing and designing your mechatronic system or subsystem, your needs and the associated competent advice are our top priority.
Due to the technically sound know-how and customer-oriented approach of our employees, as well as a worldwide network of suppliers, it is possible for us to put your desired application in the foreground. In concrete terms, this means that we tackle each of your projects regardless of technology. .
Frequently asked questions
What is the drive element?
An output element is an integral part of a drive system that is responsible for transferring the energy or torque from the drive source to an external load. These components, such as shafts, belts, chains, gears, or couplings enable the movement or rotation of the load according to the requirements of the application. The choice of the appropriate output element depends on various factors, including the type of drive, the force to be transmitted and the operating conditions.
How does an actuator work?
An actuator is a mechanism that is used to generate motion or put a machine into operation. There are different types of actuators, such as mechanical, electrical, hydraulic and pneumatic, each based on different principles. Basically, a drive converts energy into a form that is used to move or control objects.
What is a drive system?
A drive system is a complex system that is used to generate movement or put a machine into operation. It consists of various components that work together to convert an energy source into a mechanical movement. Typically, a drive system includes motors, gearboxes, drive shafts, belts or chains as well as control and monitoring units, depending on the application and type of drive.
What is drive technology?
Drive technology refers to the field that deals with the design, development and application of systems for generating motion. This includes a variety of technologies and methods used to set machines in motion or generate motion, whether by mechanical, electrical, hydraulic, or pneumatic means. Drive engineering also includes the analysis and optimization of such systems in terms of efficiency, performance and reliability.
From evaluation to series production
Antrimon supports its customers in every phase of their project with extensive specialist knowledge and many years of experience in the field. With a deep understanding of the drive market and highly qualified experts, we accompany you from evaluation to series production. Our work can start as early as the development and design of mechatronic systems to guarantee drive systems that work in practice for specific applications.
Our broad know-how and strong, long-standing partner network lead to excellent results. With our second source strategy, which includes a worldwide network, we ensure that you have the option of switching to the alternative solution at any time. We also have an in-house production facility where we assemble feedback systems on motors and assemblies and even manufacture complete devices for you.
This enables us to provide you with optimum support, regardless of whether you need individual motors, assemblies or complete drive solutions.
Technology-independent and flexible
Antrimon is focused on finding the best solution for its customers. This is why we approach projects in a technology-independent and needs-oriented manner. Our broad product portfolio covers a wide range and includes electric motors up to approx. 10kW power as well as other drive components such as gearboxes, feedback systems and various electronics for their control. The portfolio is completed by a wide selection of couplings. All this for rotary or linear solutions, equipped as DC or AC versions.
Thanks to our broad product range, we can offer numerous variants of drive solutions and adapt them flexibly to the requirements of a wide variety of applications. From drive technology to individual components - we can supply the right solution for every requirement.
Electric motors in focus: innovation and technology
Electric motors are a basic requirement for modular mechanical engineering and play a central role in modern drive technology. As the core of the drive train and important drive elements, they have a major influence on the functionality and efficiency of the drive technology and therefore the machine. Here at Antrimon, we offer an extensive portfolio of motors and various drive technology components for different applications.
The technology behind electric motors has made significant progress in recent years. Control and power electronics are technological developments that extend the performance spectrum of electric motors. In particular, the development of electric motors for electric vehicles has led to a number of innovations that further improve the performance and efficiency of these motors.
Progress in electric motor technology
A significant advance in electric motor technology is the improvement in the slot fill factor and adapted winding geometries, which lead to more efficient use of material and space within the motor. This increases the performance and efficiency of electric motors.
We are always on the ball and ensure that the latest developments lead to an increase in production quality in your specific area of application. These advances in electric motor technology allow us to produce more efficient, more powerful and more environmentally friendly motors that can be used in a wide range of applications.
Selecting the right stepper motor
Choosing the right electric motor can be a challenge, as various factors need to be taken into account. But don't worry! At Antrimon, we specialize in supporting customers from the idea phase through design to series production, offering project-optimized, cost-optimized and quality-optimized drive solutions.
Whether you need an electric, three-phase or DC motor, we can help you find the right drive for your application.
Performance requirements
The performance requirements of an electric motor are decisive for its suitability under specific load conditions. The required torque, the required speed and the maximum power of an electric motor are decisive.
Technical factors such as deviations of the actual speed from the specified speed as well as voltage and current availability can have an influence on the performance requirements of the electric motor. In addition, motor selection and performance requirements can be influenced by the physical size of the motor and specific requirements such as positioning accuracy, energy efficiency and budget constraints.
Energy efficiency
Electric motors can achieve efficiencies of up to 99%, resulting in lower energy consumption and higher efficiency. This is particularly important as, for example, around 8 billion electric motors consume almost 50% of the electricity generated in the EU, which has a significant impact on the total cost of ownership.
Replacing old electric motors with new, more energy-efficient models significantly reduces the operating costs incurred during use. But be careful - overloading and sub-optimal operating points for electric motors lead to efficiency losses and can damage the insulation capacity of the motor windings due to additional heat. It is important to design the motor correctly for the application in order to operate the motor within the permissible operating range.
Applications of electric motors
Electric motors are designed to drive gears or mechatronic applications. At Antrimon, the products are offered in different quantities, from single units to large series. They are used in a wide range of industries, including
- Pump systems
- Robotics and automation
- Building automation
- Medical technology
- Metalworking industry
- logistics
Thanks to the versatility of electric motors, from 2-pole to multi-pole construction, they offer high flexibility for different applications, for example brushless DC motors or asynchronous motors, which can be used for applications with high speeds or also at low speeds with high output torques.
Industrial applications
In industry, electric motors are essential for the operation of many machines and devices, such as fans and conveyor belts. In process automation, electric motors are used to move and operate mechanical components of production lines. The requirements for motors in the food industry and medical technology are particularly high. They must meet hygiene, watertightness, corrosion and heat resistance requirements. Miniature electric motors in medical technology must meet high requirements in terms of miniaturization, efficiency, precision and reliability, including sterilizability. They are characterized by low vibrations and high energy and power density, which makes handling easier for medical personnel.
By using control electronics in combination with highly efficient electric motors, operating costs can be reduced by over 20% in certain systems.
Maintenance and servicing of electric motors
The maintenance and servicing of electric motors is crucial in order to:
- Reduce downtimes
- Reduce the error rate in processes
- Save costs in the long term by preventing faults and defects in industrial plants.
Common problems and solutions
Electric motors are powerful and reliable, but they can also cause problems. Recurrent overload leads to motor failure. Voltage unbalance and total currents in three-phase systems can cause overheating and damage to the motor insulation.
There are many causes of failure in electric motors, but some of the most common are
- Overheating: this can be caused by overloading the motor, inadequate ventilation or poor heat dissipation.
- Bearing wear: The continuous rotation of the motor can cause bearings to wear out over time, which can lead to failure. Impacts on the abrasion of the motor can also lead to pre-damage to the bearings.
- Electrical problems: These include short circuits, winding damage, insulation faults or problems with the power supply.
- Moisture and corrosion: If moisture penetrates the motor, this can lead to corrosion and impair the functioning of the motor.
- Insufficient lubrication: Insufficient or incorrect lubrication of moving parts can lead to increased wear and breakdowns.
- Mechanical damage: This can be caused by improper operation, shocks or external impacts that affect the structure or function of the motor.
Preventive measures
Certain preventive measures are required to prevent problems with electric motors. Safety clutches protect the mechanics and prevent damage that can be caused by mechanical overload or a defective clutch.
Another important aspect is current limiting. It protects the motor winding from overheating and thus extends the service life of the motor. With these measures and the use of condition monitoring, you can optimize the performance and reliability of your electric motors and avoid expensive downtimes. Regular maintenance and inspection can help to identify and prevent these causes of failure.
Electric motors and environmental compatibility
Compared to pneumatics, electric motors are more efficient and environmentally friendly. They consume less energy and produce less waste, making them a sustainable choice for many applications. In addition, electric motors can be repaired, which extends their service life and contributes to sustainability.
Recycling and disposal
The metal components that are important parts of electric motors are over 98 percent recyclable, which enables their reuse and promotes sustainability. This also includes the reuse of copper, which plays an important role in the manufacture of electric motors.
By recycling electric motors, we can not only save valuable resources, but also reduce the amount of waste that ends up in landfills. This is an important step towards a more sustainable and environmentally friendly industry.
Summary
In this article, we have explored the world of drive technology and Antrimon's role in this field. From evaluation to series production, from choosing the right electric motor to maintenance and servicing - we have seen how Antrimon supports its customers and offers customized drive solutions. With their versatility, efficiency and environmental compatibility, electric motors play a central role in modern industry. Through continuous innovation and technological advances, they help to improve the performance and efficiency of our equipment, machines and systems. In this way, they enable us to meet the challenges of today and open up the opportunities of tomorrow.
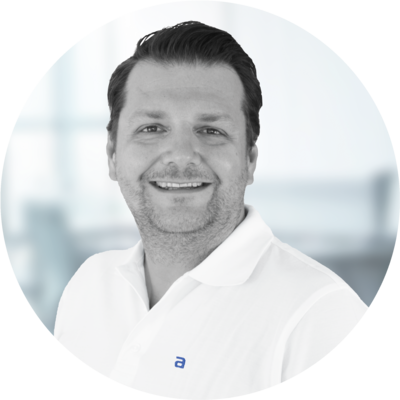